Increase Supply Chain Agility by Planning Ahead
Scenario planning is vital in order to pivot through unforeseen obstacles
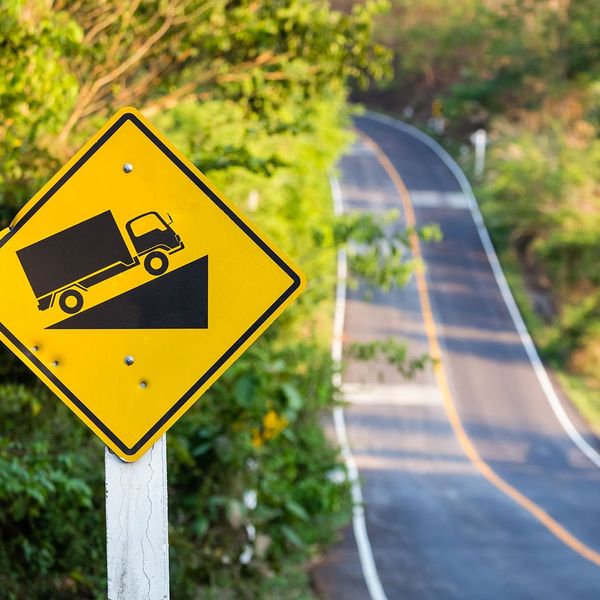
Natural disasters, supply chain bottlenecks and infrastructure challenges can all disrupt the movement of goods, and shippers are looking for ways to adapt to unforeseen circumstances, respond to disruptions and increase agility.
“Coming out of the pandemic, everyone in the supply chain is a little bit shell-shocked and thinking about what’s next,” said Amy Ilyes, vice president of logistics engineering for Penske Logistics. “Everyone needs a contingency plan. If you have done some type of planning and examined different scenarios and costs, you know the highest risk areas of your supply chain and can pivot to the most advantageous scenario.”
Contingency Planning
Data, the technology to run what-if scenarios, and supply chain visibility are at the core of an effective contingency plan. When evaluating various scenarios, Penske creates risk scores associated with different regions. “It may be a political risk or the potential for a calamity of some sort. As we look at different alternatives, we think of the risk associated with each of the network designs,” Ilyes said.
As a solution, shippers are looking to shorten their supply chains through nearshoring and adding suppliers to help reduce potential disruptions. “We can run what-if scenarios to see what the impact will be from a supply chain perspective if they nearshore or diversify their supply base,” Ilyes said.
Engineers can simulate supply chain networks using different ports, routes, suppliers, modes of transportation and inventory levels. The models help shippers determine which channels should be served by which locations, optimal supplier base locations, the best ports of entry and the ideal positions of brick-and-mortar warehouses.
The recent Francis Scott Key Bridge collapse in Baltimore, Maryland, the current drought in the Panama Canal and ongoing labor talks at North American ports have highlighted the need to identify backup ports and alternative transportation solutions. Plus, being able to react quickly is becoming even more important as customer expectations continue to rise.
Optimal Distribution Case Study
For example, in 2021, an agriculture, turf and construction equipment manufacturer was seeking solutions to pandemic-induced disruptions. By leveraging route modeling software to analyze historical and forecasted data, a new optimized distribution model was identified for maximum product availability.
A strategic overhaul of the manufacturer’s network engineering improved their lead times and freight costs. Penske managed this by:
- Changing the port of entry for specific construction equipment from Savannah to Baltimore
- Optimizing freight into multistop truckloads direct to dealers closer to the Baltimore port
- Bypassing the national distribution center for equipment, reducing lead times by eight days
Transforming the distribution process also enabled the manufacturer to cost-effectively bring equipment to market faster, boosting their market share as a result. Bypassing the national distribution center serving the northeast market also eliminated eight days of transit time.
No one could have predicted the Francis Scott Key Bridge collapse in 2024 — but because Penske makes it a practice to conduct continued network design evaluations, the manufacturer was able to quickly divert shipments to an alternative in Norfolk, Virginia. This port was identified in a previous engineering study as a cost-effective solution to transitioning away from Savannah and only added one to two days of transit time versus halting distribution altogether at the Port of Baltimore for an extended period.
Having a contingency plan is crucial to be able to pivot in times of uncertainty. In some instances, such as a port closure, business can be halted and even shut down entirely if a backup plan is not quickly enacted.
Diligent contingency planning enabled Penske to provide value to the manufacturer with:
- A $5 million cost reduction in transportation by bypassing the national distribution center and shipping more directly
- An 8-day lead time improvement to dealers
- A market share increase with improved product availability
Now that the Port of Baltimore has reopened, the manufacturer is looking to redirect equipment imports there again.
Visibility
Visibility is also a critical tool that can increase agility. Having a comprehensive view of the supply chain enables shippers to identify suppliers, routes or regions experiencing delays and adjust operations. Visibility can also help companies manage inventory and identify the best locations to use when sourcing products.
“You want to be sure your inventory visibility is at 99.9% so you know that when an order is placed, the goods are in the facility,” Ilyes said.
Information comes from multiple sources throughout the supply chain and knitting it all together can be a challenge. “Shippers may have one provider that does warehousing and one that does transportation,” Ilyes explained, adding that Penske’s ClearChain® technology suite pulls together information to create a real-time, high-level, connected view as well as granular specifics that can inform decision-making.
Transportation Management
To help gain control of the supply chain, more and more companies are interested in managing the transportation into their facility rather than relying on their suppliers to transport goods. “We’ve had a lot of requests to help shippers unbundle the cost of the product on the transportation portion of the contract,” Ilyes said.
Shippers may not even know where their suppliers are shipping from, but Ilyes said there are opportunities to create a supplier compliance program that specifies which distribution center they ship from. “It may be one that is closer, which will give you better service,” Ilyes explained, adding that compliance programs should be audited regularly.
Evaluating the whole network — including sourcing locations, inventory levels, product demand and transportation providers — can help shippers improve the overall engineering of the supply chain, increase efficiency and build resiliency. Ilyes recommends companies review their networks and transportation providers regularly to remain flexible. “You want to be able to make changes quickly based on engineers’ feedback,” she stated.
Supply chain resiliency is a fundamental principle, and to remain competitive, shippers and their logistics providers have to be able to pivot quickly in the face of adversity.
To learn more about Penske’s tools to increase agility, contact us.