Take the Complexity Out of Sub-Assembly
Rely on Penske's expertise to optimize your just-in-sequence supply chain
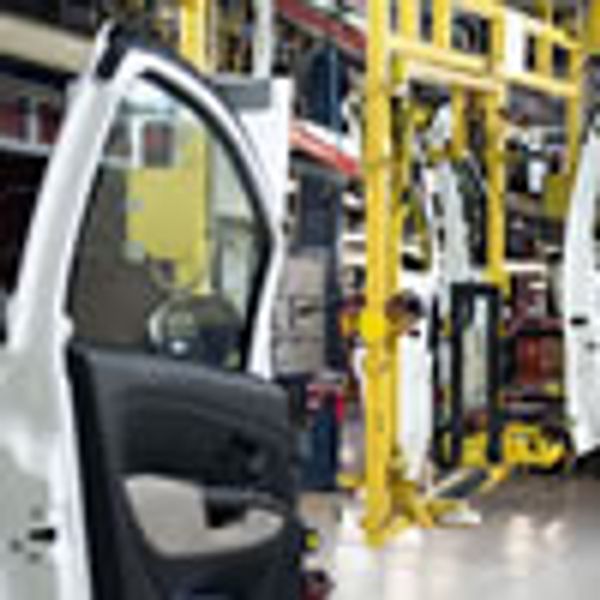
Receiving shipments on time isn't enough these days. Instead, automotive manufacturers' shipments must also arrive in the order they are needed. To do so, a manufacturers' just-in-sequence supply chain must be optimized.
Have a Plan for Every Part
Penske uses its ClearChain® technology suite to manage the sequencing and sub-assembly process, ensuring parts will arrive at manufacturing facilities on time and in the proper order. ClearChain provides a high-level and detailed view of every supply chain movement. It also uses checks and balances to bring order to even the most complex supply chains. Taming a complex supply chain means having a plan for every part (PFEP).
Eliminate the Guesswork During Picking
The sequencing and sub-assembly process begins within ClearChain when a customer sends an order via an electronic data interchange (EDI) to the warehouse management system (WMS). The WMS dictates what to pick and when. Next, the order is picked using a pick to light system, and the barcode or the paperwork associated with each item is scanned.
When an item is picked correctly, the picker receives a beep with a green light. When it's scanned incorrectly, the picker gets a red light. After picking, racks are loaded onto the trailer in reverse order, so they can be unloaded as needed at the manufacturing facility.
Use Dashboards to Monitor Each Step
ClearChain uses color-coded dashboards with red, yellow and green indicators help managers understand the status of loads – and intervene as necessary. The dashboards track the movement of goods. They also monitor sequencing. By overlaying labor dashboards in the sequencing cell, Penske monitors builds-per-hour and identifies if sequencing is falling behind.
Through ClearChain, the transportation management systems (TMS) and WMSs synchronize, enhancing visibility, improving the flow of goods and increasing efficiency. Within minutes, ClearChain technology can track every product for a shipper and provide real-time status updates.
Eliminate the Need for Buffer Inventories
Since ClearChain facilitates visibility and reliable deliveries, manufacturers can eliminate the need for buffer inventories stored on-site near the production line. That means the manufacturing facility only needs to store sequencing racks, eliminating the storage of parts and reducing the amount of space needed. Penske can create sequencing plans for the upcoming week or the next day, depending on the manufacturers' forecast – and can quickly adjust those plans based on the demand for a given day.