Manufacturers Seek Improved Supply Chain Resiliency
As manufacturing supply chains grow in complexity — so do risks
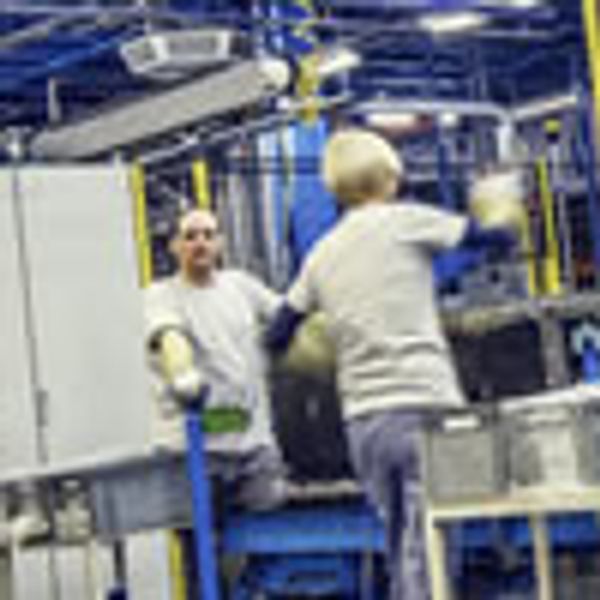
Risk management in the manufacturing supply chain has improved markedly over recent years, thanks largely to better managerial approaches, technological advances and changes in global trade patterns.
However, companies still face many challenges. The complexity of industrial manufacturing operations and a volatile competitive environment constantly threaten the integrity of supply chains.
Further advances will help companies to mitigate these risks. Technologies are being deployed to identify threats and tackle them before they turn into costly disruptions.
A Better Outlook
As supply chains expanded their global reach and became exposed to a wider range of risks, companies responded with more robust programs for managing risk.
Innovative risk management tools are a key part of these programs. For example, Penske Logistics developed a crisis management tool in collaboration with leading manufacturers in the U.S., that incorporates analysis of weather forecasts and other key predictors of operating conditions, explains Jeff Bullard, senior vice president of operations, Penske Logistics. The tool enables companies to anticipate adverse changes and re-route material flows accordingly.
A shift in outsourcing strategies also has helped to lower risk levels in supply chains. A decade or two ago, outsourcing manufacturing operations to contractors in low-cost countries was a top priority for many companies. "There was a big push to set up in countries such as China," says Bullard.
Today, this strategy commands less attention due to factors such as higher labor costs in China. Now, there is more emphasis on manufacturing in countries closer to end markets, hence shorter supply chains. "By decreasing the distance that product is moved, you also decrease the risk," says Bullard.
Problems Remain
While today's manufacturing operations are generally more resilient, they are far from risk-free. Supply chain visibility has improved, but the view remains restricted — particularly in end-to-end global supply chains. Visibility limitations create risk.
Compliance is another area where blind spots can render companies vulnerable to supply interruptions. Monitoring the performance of vendors deep within a multi-tier supply chain remains a challenge. This type of risk can increase when suppliers are widely dispersed and networks are subject to churn.
Large supplier networks also can insulate individual vendors against the end-to-end implications of risk. Small to mid-size enterprises that do not have the resources to closely monitor the supply chain are especially prone to this phenomenon. "They may be unaware of how a misstep can reverberate through the entire supply chain," says Bullard.
The volatility of today's operating environment also raises the risk profile of markets. For example, political risk is ever-present; fractious NAFTA (North America Free Trade Agreement) negotiations between Canada, Mexico and the U.S. and the protracted Brexit (the UK's exit from the European Union) negotiations in Europe are current examples. In both cases, the outcomes of the talks have a significant impact on manufacturing supply chains in respective regions.
Inventory at a Price
Companies combat and manage risk in various ways. One of the most common is to build inventory to buffer operations against unexpected changes in demand. It's an effective management approach — but it can be expensive.
"That's why companies often ask us to help them figure out how to replace inventory with information; how to sense and respond to changes proactively," says Bullard.
It's not a new idea, but modern-day tools such as Internet of Things (IoT) sensing and predictive analytics have taken it to a much higher level. Using data from an array of sensors in the field that monitor the location and status of product moving through supply chains, predictive models analyze product flows and forewarn companies of problems. Armed with this information, managers can take corrective actions that prevent problems from materializing, thereby reducing the need for costly buffer inventory.
"These systems also help us to better understand supply chain risk and ways to mitigate or eliminate it," says Bullard.
A new generation of transportation management systems (TMS) is another innovation that gives companies a clearer window into supply chain operations. Again, the solution is by no means new, but recent advances have extended TMS analytical capabilities and integrated them with other complementary technologies.
For example, the latest TMS suites marry data derived from the system with business intelligence frameworks, explains Bullard, to analyze the broad impact of occurrences such as supplier failures. "Not long ago, companies didn't have this technology. Now they can use it to map suppliers in a systematic way and evaluate the scale of potential problems," he says.
Untapped Potential
Such tools will become even more sophisticated over the next few years. Existing technologies such as IoT sensing are being refined, and newer ones — Blockchain being the most notable example at present — promise to bring new capabilities.
"In some areas, we are only scratching the surface; the potential for improving risk management in the manufacturing supply chain is immense as these technologies evolve," says Bullard.