Resolving Problems in Motion to Maintain Visibility at the Border
Cross border technologies can help you take control of your supply chain
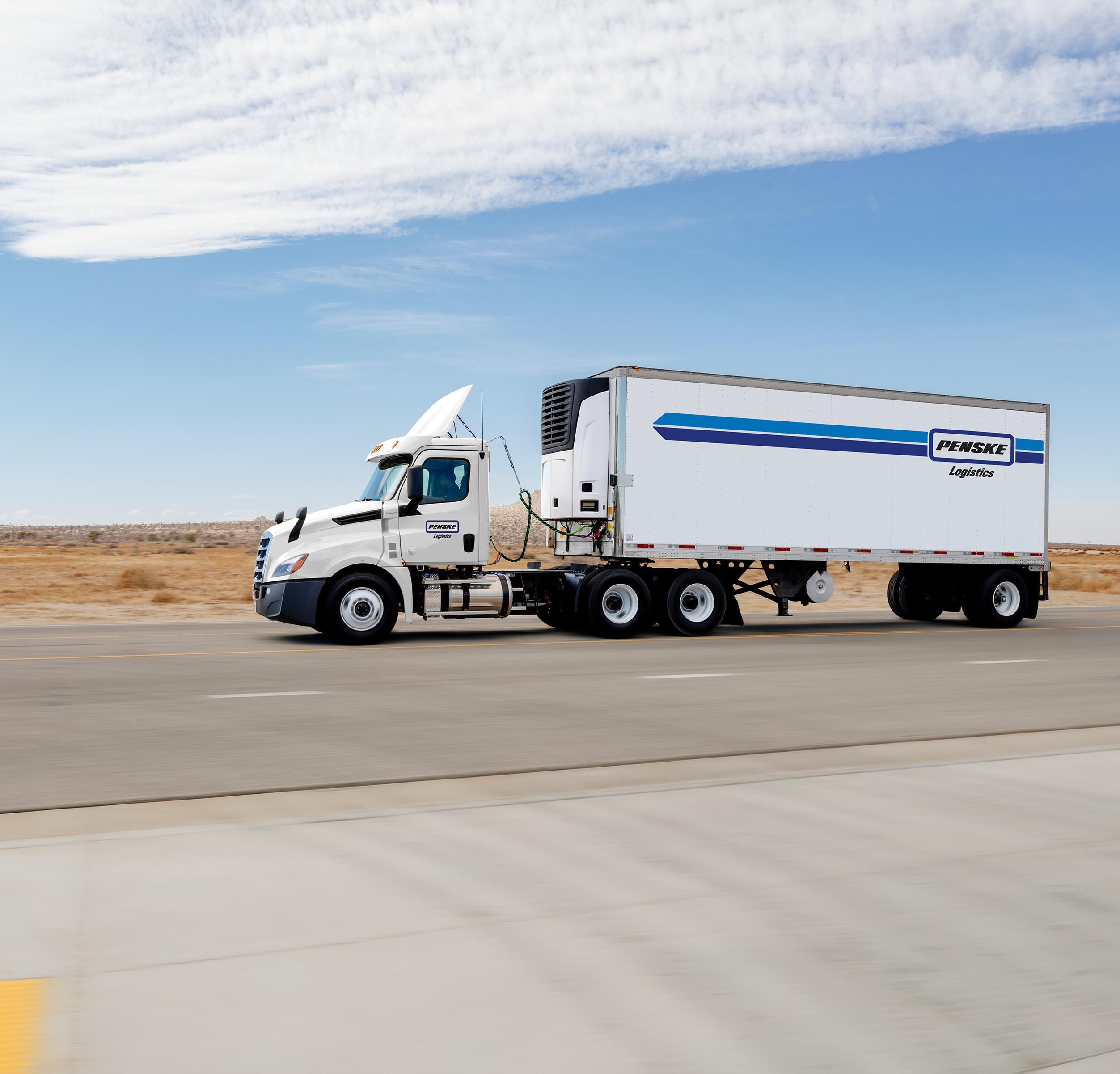
Visibility is critical at the border, and being proactive rather than reactive can keep products moving. Penske has added a border workflow technology tool as part of its ClearChain® technology suite that facilitates collaboration between the many stakeholders involved in a border crossing to mitigate the risk of a delay.
“In the supply chain, the border can be a big black hole. This technology provides transparency at the border on arrivals, paperwork, handoffs, customs clearance, carrier arrival, and we can mitigate loads getting stuck at the border,” said Ramu Pannala, vice president of supply chain technology at Penske Logistics.
How to Reduce Border Wait Time
The border application relies on three pillars — visibility, document sharing, and validation and compliance — creating a more granular level of tracking and visibility. It provides alerts and notifications to enable proactive monitoring and exception handling, which increases predictability and significantly reduces time spent at the border.
“This border management solution resolves problems while freight is in motion rather than when it comes to rest,” said Tracy Urbanski, senior vice president of operations for Penske Logistics. “With all the milestones along the shipment’s route, there are opportunities for the product to stop or gaps to happen. This management solution resolves these issues in transit, so when a trailer reaches the border, whether going northbound or southbound, there is a far less likelihood of that freight stopping.”
Cross-border loads require specific documentation, including bills of lading, packing slips, commercial invoices and certificates of origin. With all partners communicating on a single platform, those involved can receive advance notification of information and validate if it is right or wrong.
If a piece of critical documentation is missing, it creates an immediate flag. For example, in auto-related shipments, each part number must have a harmonized tariff code. “If it doesn’t, that means customs doesn’t know about it, and we will have to do research. If we can find out there is a new part number when that shipment left, we could have two days to research it,” Urbanski said.
Avoiding Miscommunication
There are multiple stakeholders involved in each cross-border shipment, and, traditionally, a lot of communication between parties takes place in emails. “There might be dozens of people included in the email,” Urbanski said. “It becomes noise inside of our customers’ email chains. Depending on their volume, they may get hundreds of messages a day, and now they’re trying to decide what issue they have and who is taking care of it.”
Scattered emails result in a lack of action-oriented information. The border application eliminates the need for email and allows all involved to see who is doing what. “We eliminate the email, so everybody is working in the platform together,” Urbanski said, adding that the technology also creates accountability.
Maintaining Data Accuracy Amid Changing Regulations
One of the biggest gaps Penske has identified is miscommunication between when customs paperwork was completed and when the drayage carrier arrived for pickup. Often, the drayage carrier wasn’t clear on the status or didn’t receive the message, delaying arrival. “Now the paperwork is uploaded in the system, it is time-stamped, and the carrier team is able to see it. We’re measuring the time from when the customs paperwork was ready and when the drayage provider picked it up. There is no more confusion,” Urbanski said.
Changing regulations in Mexico have the potential to create more complexity, making connectivity and visibility between shippers, brokers, freight forwarders, carriers and all the stakeholders dealing with border crossings even more important.
Data security is a top priority, and the border application uses encrypted messages and rule-based security to ensure the integrity of the data being shared.
With tools to ensure visibility, Penske can keep freight moving at border crossings while maintaining security and compliance. Having the ability to mitigate and resolve problems while freight continues to move is a game-changer, and with open communication and collaboration on a single platform like ClearChain, you'll spend less time at the border and more time moving forward.
To learn more about Penske’s scalable border solution, contact us.