An Efficient Warehouse: More than Just Software
Implement an Effective Labor Management System
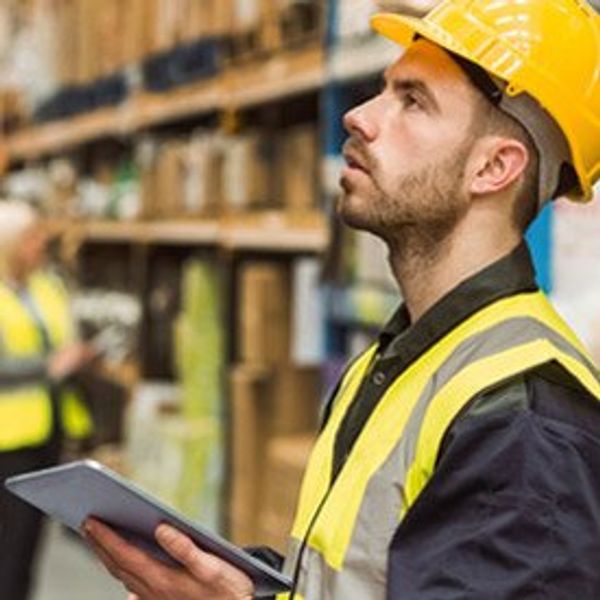
Many organizations scramble to purchase costly warehouse management systems (WMS) in the hopes of solving all their warehouse challenges, only to be disappointed when the system fails to meet their expectations.
Labor management combines software and engineering to maximize user performance and warehouse utilization. The key to making the program launch a success is keeping the lines of communication open and making sure the associates are kept in the loop at every step.
Implementation of an effective labor management system requires a measured process that allows ample time for employees at all levels to integrate the new requirements into their behavior and to see the benefits of the initiative.
While standard approaches focus on top-down management, the program used at Penske Logistics engages workers at the employee level and empowers them to "own" the process, from implementation to communication to identifying areas for improvement and best practices for all processes within the warehouse.
As part of the implementation process, employees and engineers are required to develop discrete, multi-variable labor standards for each process, taking into account all process steps required while performing the task.
Associates have the opportunity to develop leadership qualities by training management on coaching techniques, thus removing barriers that may exist between management and work force. By utilizing the software collectively, there is more buy-in across the levels in the organization, creating more of a "flat" organizational environment.
As a group, associates implement relevant incentives as a reward for top performers. They accept the parameters because they helped shape them and have a stake in their success.
It must be clear that the emphasis on productivity does not come at the expense of quality or safety and that foremost emphasis must be placed on the attention to quality and safety in all aspects of warehouse activity.
In creating the culture for an effective labor management environment, the preferred methods are to:
- Establish labor standards
- Standardize and streamline operations
- Eliminate activities that are deemed by employees to be non-value-added
After this step comes leadership training, where the local supervisors and managers are empowered to lead from the front and understand and change the process. Mentoring is very important throughout the implementation of a labor management program. Mentors need to observe, coach, provide feedback and evaluate. Local leaders should foster the development of associates with effective guidance.
In order to track performance, the direct labor functions will be monitored and there should be increased visibility into individual and team productivity, in addition to the ability to track expenses to individuals.
Motivation is easy with this program; performance tracking increases visibility at both the individual and team levels, which requires accountability and provides recognition and reward.
The value of the labor management system is evident in terms of associate relations, management effectiveness and operations effectiveness.
Associate Relations Value
- Timely, objective feedback of associate performance
- Increased associate earnings with no risk to the labor budget
- Improved attitude and morale
Management Effectiveness Value
- Provides management tools and techniques for staffing, goal-setting and reporting
- Comprehensive management training
- Ability to attract and retain top-quality associates
- Enables management staff to effectively display the value brought to the customer
Operations Effectiveness Value
- Maximum utilization of work force
- Appropriate manager/associate ratios
- Extended facility throughput and capacity
Labor Management Software Implementation
Phase I - The labor management program is best rolled out through a phased implementation over the course of about four months. The program is launched with a kickoff meeting to explain the scope and plan to employees. During the first month, management will seek employee buy-in and allow the concept and its benefits to sink in so that upon implementation, employees will embrace it with a positive attitude. In addition, during this phase, baseline labor analysis is completed, allowing for effective measurement of the launch.
Phase II - Implementation begins with the largest labor buckets, e.g. picking and put-away
Phase III – The rollout proceeds to medium labor buckets, e.g., unloading, loading, in/outbound scanning
Phase IV – The final phase of the program begins with indirect labor buckets, e.g., returns processing, consolidation and cycle counting
Once all standards for the major functions have gone live, the program will require ongoing support for standard maintenance, accountability and performance improvement planning, continuous improvement initiatives and weekly operations meetings.
Employees are eligible to receive incentives in two ways: as individuals and as part of a team.
To qualify as individuals, each person must:
- Have 20 qualifying hours for the week
- Achieve 101% of location average productivity score
- Be accident- and injury-free
- Work scheduled work week – no unexcused absences
To qualify as a team, each team must:
- Hit the location units per man-hour goal
- Have 99.5% stow accuracy for the previous week
- Not exceed in-house damage goal (e.g., established DPMO rate)
A Labor Management Success Story
A major appliance manufacturer was operating a 1.7Mft, dual-use facility with 150 associates. The title of its program, chosen by the associates, was "Employees 4 Success." Within the first eight months, employee productivity had increased 22% and cost-per-unit had decreased 16%. Over the course of three years, the units-per-hour had increased 31%, the cost-per-unit had dropped 41% and the damage had decreased a full 68%.
Six Steps to Assessing Your Warehouse Efficiency
1) Yard Process – You need a plan for handling the trailer before it arrives at your gate. Does it go straight to a door, sit and wait based on priority, or is it arriving as replenishment stock and only needs to be dropped off?
2) Inbound Process – The moment the product arrives at your facility you need to know where it's headed, how it needs to be handled and how long it may need to stay there. We call it a "Plan For Every Part" (PFEP).
3) Outbound Process – A big step that you can't overlook is the final piece of the puzzle – the outbound process. Two keys to shipping the perfect order are ensuring you have done all the required previous steps for handling at your location, and doing it on time.
4) Task Management – Once all available product is on hand and the work required is known, how do you prioritize what needs to be handled to achieve maximum efficiency? The most efficient way to execute this is by using your WMS as the backbone, and letting it optimize task assignments.
5) Inventory Management – Last-In-First-Out (LIFO), First-In-First-Out (FIFO), first available, cross-docked product – how you choose to stock and use your inventory will greatly affect the required handling, racking and the processes within the building.
6) Warehouse Labor – This component drives roughly 70 percent of your overall cost of doing business in a warehouse. It's easy to throw extra staff at a problem to meet demand, but the trick is planning and optimizing to minimize the single largest line item in your warehouse budget.