Boost Warehouse Capacity Without Adding Space
Strategies to get the most out of the square footage within the four walls of the warehouse
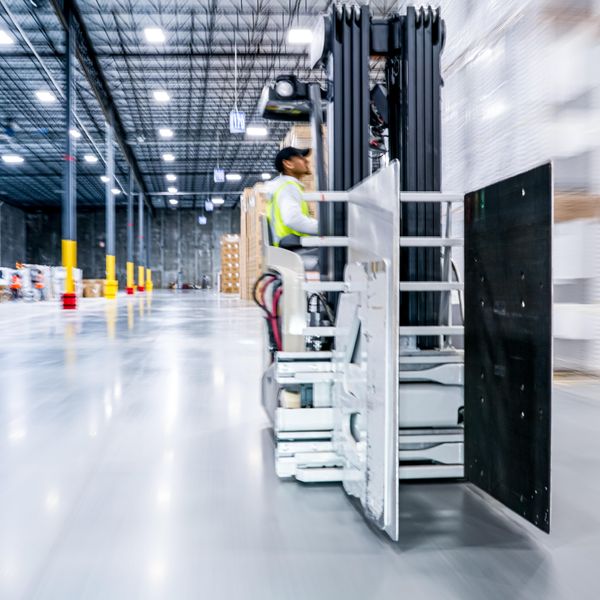
Warehousing space is at a premium and represents a significant portion of total supply chain costs. Consequently, shippers need to carefully evaluate the case for investing in more storage capacity.
There are many warehousing configurations to choose from — and the range of options has increased markedly over recent years — but a potential solution that is cost-effective is to make the best use of existing capacity.
Capacity-Building Strategies
Penske Logistics helps shippers to get the most out of their warehouses without necessarily having to invest in more square footage. Here are some examples of these strategies.
1. Keep Labor in the Loop
The cost of labor can account for up to 65% of total warehouse fulfillment costs depending on how a facility is owned and managed. And these costs can increase significantly in tight labor markets.
Moreover, the way a warehouse workforce is trained, deployed and managed has a huge impact on the facility's productivity. At Penske, "Labor management combines software and engineering to maximize user performance and warehouse utilization," says Andy Moses, senior vice president of solutions and sales strategy, Penske Logistics.
The key to a successful program is "keeping the lines of communication open and making sure the associates are kept in the loop at every step," he says.
Such an approach can yield multiple benefits from a warehouse capacity perspective. Here are some examples.
- Improved planning. With better visibility into the volume and types of work being performed, a shipper can more effectively plan a facility's workforce requirements to meet operational demands. Better planning also supports a more balanced workforce that is attuned to variations in operational demands.
- More effective reporting. Giving the workforce visibility into their own performance, and performance at a team level, encourages competition and identifies drivers of efficiency. More visibility also promotes associate accountability.
- Adherence to preferred methods. With established labor standards, operations can be standardized and streamlined, which helps to eliminate non-value-added activities.
Penske helped a major manufacturer that operated a 1.7 million square-foot, dual-use warehouse with 150 associates to implement a labor management program. Within the first eight months, employee productivity had increased by 22%.
2. Make Quicker Picks
Speeding up picking operations is an effective way to improve the utilization of a warehouse.
For instance, warehousing operations can be optimized "by implementing systems that put inventory in bulk locations first and then replenish to active locations to pick orders at ground level to increase pick speed," says Don Klug, vice president-sales, Penske Logistics. Introducing wearable scanners and/or voice picking are other ways to drive up pick speed.
3. Optimize Slotting
Another critically important component of a warehouse that can be reengineered to maximize capacity is a facility's slotting system.
"One of the biggest services we provide for any customer is slotting analysis," said Klug. Improving slotting methodology improves warehouse utilization as well as the efficiency of fulfillment operations.
A slotting analysis typically starts by identifying volumes and categorizing SKUs according to how fast they move through the warehouse. Category A products move the fastest, followed by B and C-class SKUs that move slower and slower still. A-class products are stored closer to the dock to minimize travel, whereas C-level items are located further from the dock or in higher locations where there are racking systems.
Penske engineers analyze inventory movement over time, taking various factors into account such as seasonal variations in throughput. The findings are translated into rules that drive the warehouse management system (WMS). Over time, the rules are refined, and the WMS updated.
Slotting patterns can be changed in line with shifts in demand. Some industries, such as food and beverage, change slotting patterns seasonally. "Strawberries sell at specific times of the year, so you'll open up a part of the warehouse to store them for more efficient put-away and picking," says Klug.
4. Tailor the Space for Efficiency
Choosing the most efficient layout for the mix of products being stored helps shippers to maximize the productivity of warehouse facilities.
Consider, for example, floor storage space. A standard aisle width might be 12 to 14 feet between product rows to allow forklifts to move smoothly. That distance can drop to 8 to 10 feet if a reach truck is used. "If you go to VNA (very narrow aisle), around a 6-foot aisle, you need a wire-guided solution, which requires wires to be installed in the floor at the center of each aisle as well as wire guidance on the material handling equipment."
Alternatively, racking systems that utilize the vertical space in the warehouse may be a better option. As Klug explains, Penske can design and install single-deep, double-deep, push-back, or drive-in racking systems to add storage locations in a warehouse.
Keep Moving Forward
The above strategies help shippers to use every square foot of space in their warehouses — but the effort should not stop there.
Building on these strategies with a continuous improvement program can yield more capacity-boosting opportunities.
Penske offers multiple options such as the Kaizen+ program, which trains every associate and load planner to look for ways to eliminate wasteful processes and practices. There is a workflow to submit ideas, and improvements are tracked so that best practices can be shared.